Apparel & Textiles
Best Quality Inspection Services
Apparel & Textiles
Reach your quality objectives, deliver safe products to customer with best quality as well as meet contractual deadlines with cutting-edge, tailor-made, quality control solutions for Softlines
All-inclusive
From us$198
Book Now
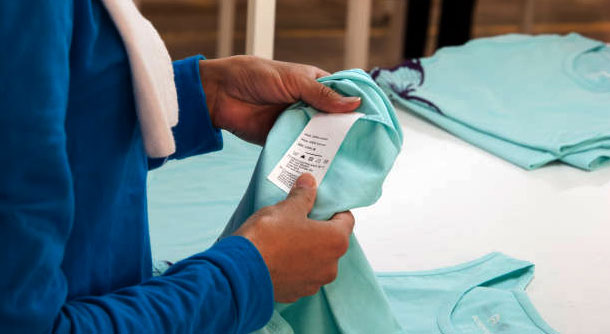
At BQIS, we understand the importance of producing high-quality products that meet industry standards and regulations. Whether you are sourcing fabric material from China or buying apparel from India or Vietnam or Pakistan. We offer a comprehensive range of quality control services designed to mitigate risks and ensure compliance.
Whether you use in-house quality control inspectors or a third-party QC service, here are five fundamental steps that a garment inspection procedure must include:
.
1. Measuring garment dimensions
Your consumers want clothes that fit well and are true to size, which is why measuring garment dimensions is absolutely crucial for quality control. The dimensions of your garments must be consistent and comply with their specified sizes. It’s important to remember that discrepancies in dimensions can exist even in precise manufacturing processes. Meanwhile, apparel manufacturing still involves many manual steps, which makes the margin for error much greater. To conduct this test, the quality control inspector takes measurements of the different parts of the garment being checked and compares them against your specifications. This is done for every clothing size in your order. To make sure this check is carried out properly, your garment specifications should clearly state the points of measurement (e.g., sleeve length, neck width), the standard measurements for each size, and acceptable tolerances for each point of measurement.
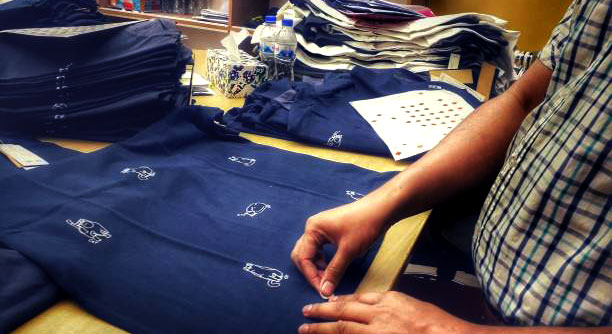
Specifying tolerances for garment dimensions
QC inspectors and your supplier should be well informed of the tolerances for garment dimensions, which determine an acceptable margin of error for any defects or discrepancies. Tolerances can vary for different parts of the garment, depending on their significance to the entire piece. For example, ¼ inch may be an acceptable margin of error for a shirt’s chest width measurement, but the same shirt’s sleeve being too short or too long by the same ¼ inch would be marked a fail. The tolerances for every point of measurement should be clearly specified on the QC inspectors’ checklist.
Fit test
A garment that matches its specified dimensions is likely to look as intended when worn, but a human body is a complex shape, and correct measurements don’t always guarantee the final garment’s correct fit and look. This is why a fitting test is an important part of the garment quality inspection procedure. To carry out the fitting test, a quality control inspector will place the checked garment onto a mannequin of appropriate size, and perform a visual check. The garment should sit on the mannequin properly and look as per the reference pictures provided by the brand.
Unreliable accessories can destroy the consumer’s overall impression of your product and brand. No one wants a garment with buttons that come loose after a day, zips that break after little use, or decorations that get ruined in the first wash. This is why the quality of your garment’s accessories can become the yardstick by which your consumer judges your product’s quality. At the same time, this crucial area is often where manufacturers might choose to cut corners and costs by buying low-quality accessories. In addition, issues with buttons and buttonholes can indicate poor stitching. QC inspectors use a variety of physical tests to identify possible defects with garment accessories such as zippers, snaps, ribbons and elastic. The tests are performed on a designated number of garments in each batch. Below are some examples.
Pull test
Predominantly used to test zippers. In this test, a QC inspector uses a gauge to pull on the accessory with a predetermined amount of force for 10 seconds.
Fatigue test
This test determines whether the accessory will last as long as intended under normal use by the consumer. A typical test on snaps or buttons would be to repeatedly button and unbutton the accessory 50 times and check for any damage to the garment after testing.
Stretch test
This check is carried out to test elastic bands and straps for proper elasticity, and to check whether the elastic or stitching stands up to being pulled or stretched. Stretch tests only need to be carried out on a small selection of finished garments.
3. Garment appearance, workmanship and other checks
This category covers a number of quality inspection procedures that ensure that the tested apparel meets your specifications and functional requirements. Such garment tests may include:
- Checking garment style and colors against an approved sample: inspectors will use photographs and Pantone color charts for comparison
- Checking any artwork or logos: to ensure that any artwork and/or logos match the reference, are properly positioned on the garment, and appropriately attached (stitched on, glued on, etc.)
- Stripes check: if the garment is made of striped fabric, this check makes sure that it was cut and sewn properly, so that the stripes match up at the seams
- Needle detection check: the garment is passed through a metal detector to ensure no needle fragments were left behind, as these can cause serious injury to consumers
- Rub tests: to check colorfastness
- Seam slippage test (for woven garments): used to check whether the fabric will slip at a seam when stress is applied, which is usually caused by poor fabric design, narrow seam margin, or not enough stitches per inch
- Odor tests: to ensure the garment is free of moisture and mold, and other contaminants that may cause an irregular odor
4. Label verification
Correct labeling is essential for complying with the garment labeling requirements of your destination markets. The EU and United States in particular have strict regulations regarding garment labeling, and incorrect or missing labels can see your product rejected at customs, or land you with a fine. You should always check your destination market’s specific labeling requirements, but as a rule, the garment label should contain the following information:
- Fiber content of the garment
- Country of origin
- Information about the manufacturer / importer / distributor
- Garment sizing
- Care instructions for washing and ironing
There are specific labeling requirements for wool, leather and fur garments, as well as for footwear, where labels must specify
Barcode scanning test
Correct barcodes on shipping and retail packaging are essential for tracking your shipments, and for quick processing of your products at distribution centers and points of sale. However, issues with barcodes are found very frequently during QC inspections. Barcode scanning test should be performed as part of both the labeling check and the packaging check, because the barcodes on retail packaging and those attached to shipping cartons serve different purposes and contain different information. As part of the barcode scanning test, a quality control inspector uses a barcode scanner device or app to ensure that your product’s barcode is:
- Linked to correct information
- Properly printed and readable
- Appropriately sized
- Properly orientated
- Not damaged or distorted
One of the final on-site inspections for garments before shipping from the factory is to ensure the packaging is suitable to protect the products in transit and in compliance with the destination market’s regulations. Lack of attention to packaging can result in your shipment being delayed, lost or turned away at customs, or the products becoming damaged.
During a packaging check, an inspector will answer such questions as:
• Is the correct number and assortment packed per carton?
• Is the shipping carton an appropriate size, weight and material?
• Are inner cartons or individual polybags properly sealed?
• Does the carton adequately protect the products inside it?
• If polybags are used, do they include proper warnings as required by the destination market?
• If desiccant sachets are used (e.g. silica gel), are they in compliance with the consumer safety laws of the destination market?
• Are shipping marks correct, properly attached and legible?
• Are the markings on the carton front and sides consistent?
• Are the barcodes correct and scannable?
Shipping marking check
Last but not least, the shipping marking must be carefully checked to make sure it includes all information required by the destination market. While specific regulations may vary from country to country, shipping markings will commonly need to include:
• Buyer’s name and PO number
• Item number and description
• Carton dimensions and weight
• Number of cartons in set
• Country of origin
How BQIS Can Help You
Not sure where to start your apparel quality control process? At BQIS, we offer thousands off-the-shelf quality control checklists, which can be fully customized to match your product inspection needs perfectly. As a third-party QC provider, BQIS offers product inspections at different stages of manufacturing, including Initial Production Checks, During Production Inspections, Pre-Shipment Inspections, and Container Loading Checks. Being independent of any sourcing operations, we provide objective and impartial information that you can trust. Our product inspectors are dispatched to your supplier’s factory anywhere in the world within 48 hours. You receive detailed inspection reports with pictures the same day, and can easily make an informed decision whether to approve the shipment.
Contact us today to discuss a garment quality control program that will be a perfect fit for your business.
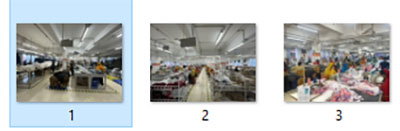
Let’s Chat
Donec sollicitudin molestie malesuada. Praesent sapien massa, convallis a pellentesque nec, egestas non nisi. Praesent sapien massa, convallis a pellentesque nec.